Grinding Wheel Neglect Can be Devastating
No one who has been involved with roller grinding doubts the importance of good wheel condition to process efficiency and quality of results. Yet, day-in and day-out, the negative affects of worn wheels occur. Failing to properly maintain your grinding wheels can lead to the following problems:
Dust Collector Fires
Low Production Rates
Quality Rejects
Lost Profit
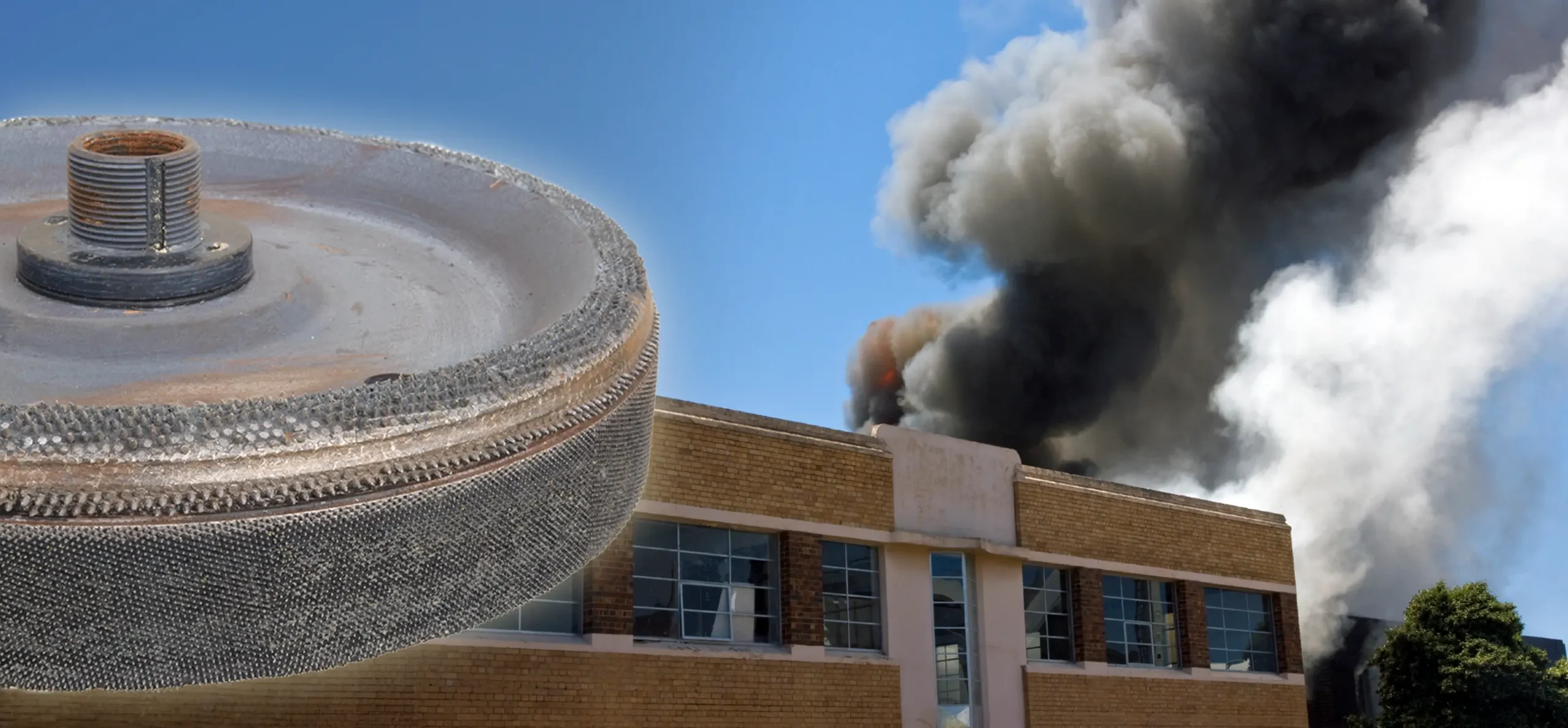
Improperly maintained grinding wheels can cause dust collector fires.
How to Properly Maintain Grinding Wheels
At Oliver Carbide Products, we are dedicated to helping you get optimum performance from your Rubberhog grinding wheels. Our booklet, How Worn is Worn Out*, describes in detail a system for better monitoring grinding wheel condition. By following this system, you can maximize grinding efficiency and avoid the disastrous problems that worn grinding wheels can cause.
Among the elements of this system, simple close visual inspection of the wheel surface is probably the easiest to apply and is very effective. The information below is intended as a shopper reference for inspecting wheel condition.
- Frequent wheel inspection
- Power monitoring
- Temperature monitoring
- Good record keeping
- Regular wheel replacement
Inspection of Wheel Condition
Wheel wear is notable by the rounding or “blunting” of the conical teeth. Wear occurs most rapidly at the corner radii where the wheel sides and OD blend, and where the fine coating starts at the “step” between coarse and fine coatings on multiple-grit wheels. With the machine power locked out, rotate the wheel slowly by hand while inspecting the surface with a simple magnifier such as a folding “linen- tester” or a magnifying visor. The teeth, when new, are very sharp, with well-defined tips. Over time, dulling produces blunt-looking tips. The dulling is usually accompanied by an obvious increase in shininess, and the teeth will exhibit very little bite when stroked with your fingertips. Usually the change in bite is highly directional; running a fingertip in the direction of rotation, and then against it, will show a marked difference in aggressiveness. The photos below show magnified views of both MCM and SSG teeth in new and worn condition.
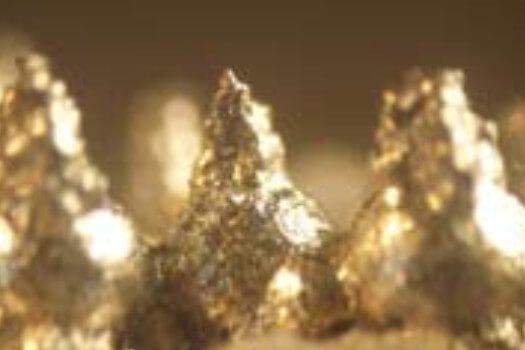
New SSG teeth
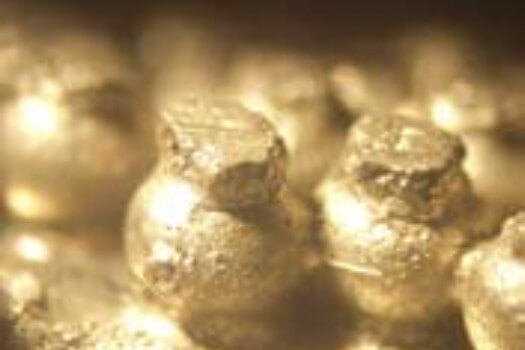
Worn SSG Teeth
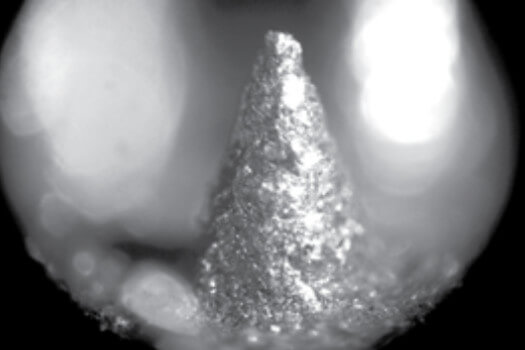
New MCM Teeth
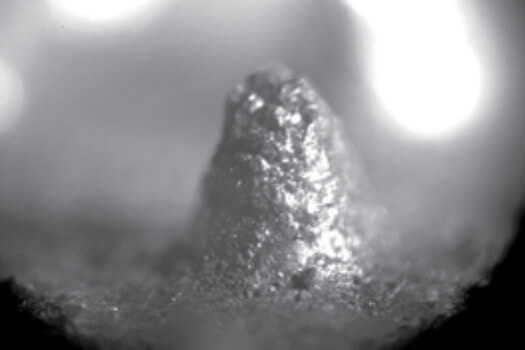
Worn MCM Teeth
Rubberhog Design Center
Rubberhog wheels are custom-designed and produced to match your machine and product requirements. Selecting and ordering the optimum Rubberhog for your application requires gathering information about your grinding equipment, the type of grinding jobs you perform, and the materials which you grind. There are four primary aspects of wheel design to consider: Physical dimensions, wheel style, coating type, and coarseness grade.